Understanding Polyurethane Foam Moulding: A Comprehensive Overview
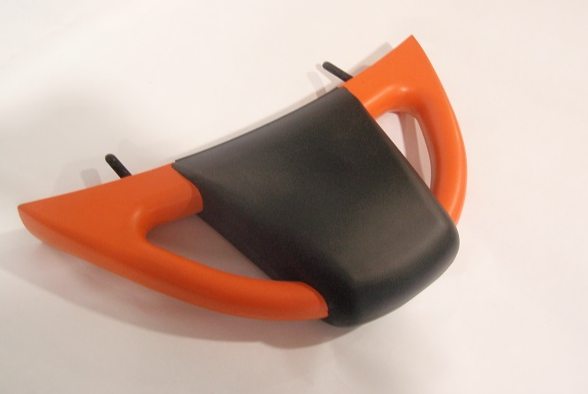
Polyurethane foam moulding stands as a cornerstone in various industries due to its versatility and unique properties. This article explores the intricacies of polyurethane foam moulding, its applications, and the manufacturing processes involved, ensuring a deep understanding of this innovative material.
Introduction to Foam Moulding
Foam moulding, specifically polyurethane foam moulding, plays a pivotal role in creating durable and versatile products. This process involves the use of polyurethane foam, a material known for its flexibility, durability, and ease of moulding. With its application ranging from industrial components to consumer goods, foam moulding has become an integral part of modern manufacturing.
The Art of Polyurethane Foam Moulding
What is Polyurethane Foam Moulding?
Polyurethane foam moulding, or integral skin moulding, is a specialized technique where polyurethane foam is shaped into various forms to meet specific needs. This process involves creating a tough, flexible skin over a micro-cellular foam core, which provides excellent protection against wear and tear. The result is a product that combines both softness and durability.
Key Features of Polyurethane Foam Moulding
- Integral Skin Formation: The moulding process creates a robust, self-skinned surface that protects the foam core.
- Versatile Applications: Ideal for components such as grab handles, armrests, steering wheels, and more.
- Customizable Textures: Mould tooling can be chemically etched to achieve different textures, such as a leather-like finish.
- Durability and Flexibility: The foam core can vary in hardness, providing a range of options for different applications.
Manufacturing Process of Foam Moulding
Detailed Process Overview
The foam moulding process involves several steps to ensure high-quality outcomes:
- Mixing: Two parts of polyurethane foam are mixed to initiate a chemical reaction.
- Moulding: The mixture is dispensed into moulds where it cures into the desired shape.
- Trimming: Excess material, known as flash, is trimmed off.
- Curing: The product is stored until it reaches its final cure stage.
- Quality Control: Rigorous checks are performed to ensure density, hardness, and other properties meet standards.
Technical Considerations
- Tool Design: Essential for ensuring accurate moulding and achieving the desired product specifications.
- Material Control: Ensures consistency in density, hardness, and other critical properties.
- Inspection and Dispatch: Finished products undergo thorough inspection before being dispatched to customers.
Applications of Polyurethane Foam Moulding
Diverse Industry Applications
Polyurethane foam moulding is utilized across various sectors, demonstrating its versatility:
- Automotive: Used in components like steering wheels, headrests, and armrests.
- Marine: Applied in seating and trim for boats and other marine vehicles.
- Office Furniture: Features in armrests, headrests, and other ergonomic components.
- Safety Products: Incorporated into protective gear and equipment.
Customization and Innovation
- Metal Inserts: Added to provide additional rigidity and strength.
- UV Stable Coatings: Applied to protect against color aging from sunlight.
- Rapid Prototyping: Allows for quick development and sampling of new designs.
Benefits of Polyurethane Foam Moulding
Key Advantages
- Durability: The integral skin offers excellent protection against physical damage.
- Flexibility: Suitable for various shapes and applications due to its adaptable nature.
- Aesthetic Options: Customizable textures and finishes enhance product appeal.
- Rapid Production: Efficient manufacturing process supports quick turnaround times.
Read Also: The Ultimate Guide to Wholesale Down Pillows: A Luxurious Addition to Your Bedding Business
Conclusion
In conclusion, polyurethane foam moulding is a dynamic and essential technique in modern manufacturing. Its ability to produce durable, flexible, and aesthetically pleasing products makes it invaluable across various industries. Whether used for automotive components, office furniture, or marine applications, foam moulding demonstrates its versatility and effectiveness. For high-quality polyurethane foam moulding solutions, Acoustafoam stands out with its expertise and commitment to excellence.
Contact Us
For more information on polyurethane foam moulding and to explore how our solutions can meet your needs, please reach out to us. We look forward to assisting you with your foam moulding requirements.